Plastic extrusion for streamlined, expandable manufacturing solutions
Plastic extrusion for streamlined, expandable manufacturing solutions
Blog Article
Understanding the Essentials and Applications of Plastic Extrusion in Modern Manufacturing
In the realm of modern-day manufacturing, the strategy of plastic extrusion plays an instrumental function - plastic extrusion. This intricate procedure, involving the melting and shaping of plastic through specialized dies, is leveraged across different industries for the production of diverse items. From auto parts to customer goods product packaging, the applications are vast, and the capacity for sustainability is equally remarkable. Unwinding the principles of this procedure reveals the real flexibility and possibility of plastic extrusion.
The Basics of Plastic Extrusion Refine
While it might appear complex, the fundamentals of the plastic extrusion procedure are based on fairly simple principles. It is a manufacturing procedure in which plastic is melted and after that shaped right into a constant account via a die. The plastic extrusion procedure is thoroughly used in various sectors due to its adaptability, cost-effectiveness, and effectiveness.
Various Sorts Of Plastic Extrusion Techniques
Building upon the fundamental understanding of the plastic extrusion procedure, it is needed to check out the different techniques entailed in this manufacturing approach. The two main techniques are profile extrusion and sheet extrusion. In account extrusion, plastic is melted and created into a continual profile, frequently made use of to create pipes, poles, rails, and window structures. In contrast, sheet extrusion produces large, flat sheets of plastic, which are commonly more processed right into items such as food packaging, shower curtains, and auto parts. Each technique needs specialized equipment and specific control over temperature and pressure to make certain the plastic keeps its form throughout air conditioning. Understanding these methods is crucial to making use of plastic extrusion efficiently in contemporary manufacturing.
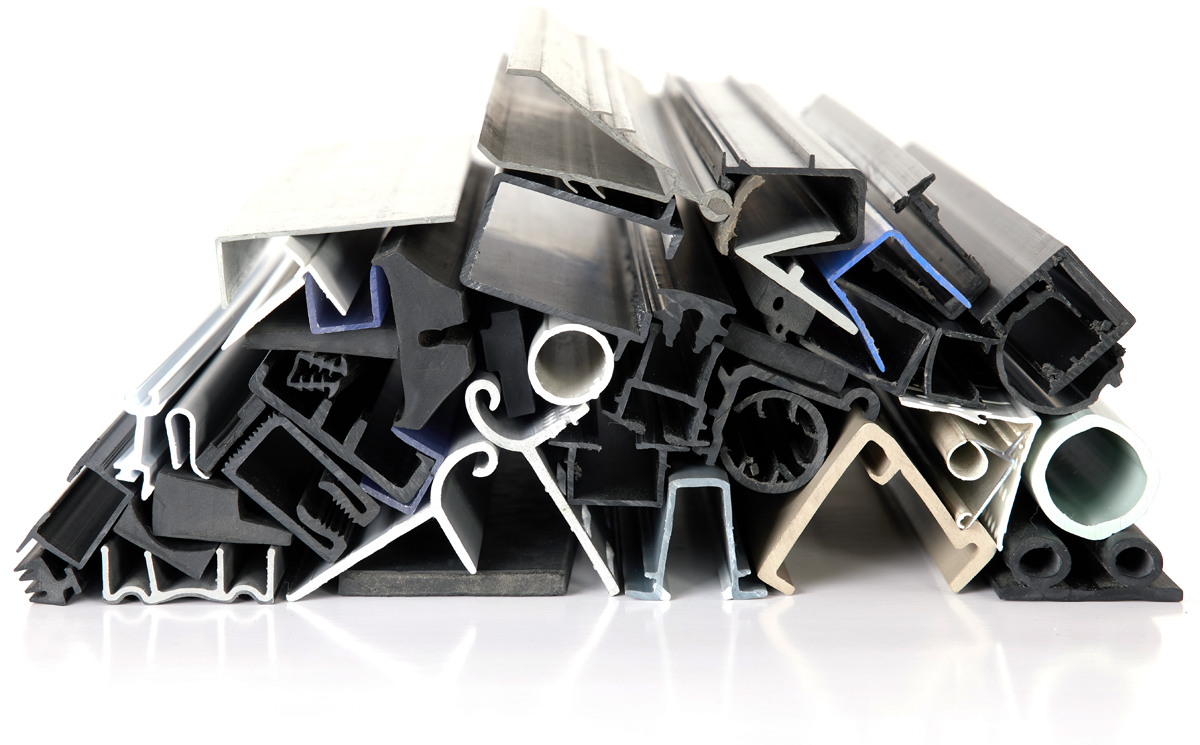
The Role of Plastic Extrusion in the Automotive Market
An overwhelming bulk of components in modern-day cars are products of the plastic extrusion process. This process has changed the vehicle sector, transforming it into a much more reliable, economical, and adaptable manufacturing field. Plastic extrusion is mostly used in the production of numerous car elements such as bumpers, grills, door panels, and control panel trim. The procedure offers an attire, constant result, allowing manufacturers to create high-volume parts with great accuracy and minimal waste. The agility of the extruded plastic components adds to the general decrease in vehicle weight, boosting fuel performance. Moreover, the sturdiness and resistance of these parts to heat, chilly, and influence boost the long life of autos. Hence, plastic extrusion plays an essential role in auto manufacturing.
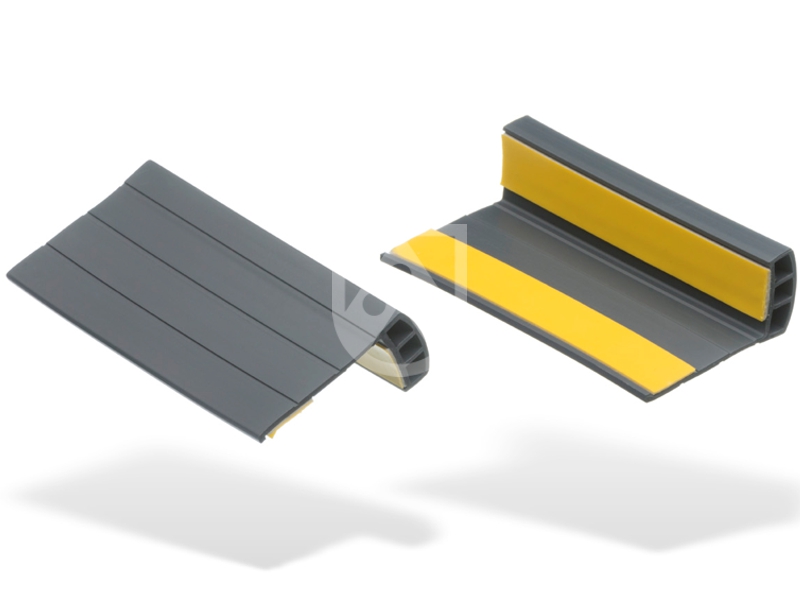
Applications of Plastic Extrusion in Customer Product Manufacturing
Beyond its significant effect on the automotive sector, see this site plastic extrusion verifies similarly effective in the realm of customer products producing. The flexibility of plastic extrusion allows manufacturers to create and create complicated forms and dimensions with high accuracy and efficiency. The adaptability, flexibility, and cost-effectiveness of plastic extrusion make it a favored option for numerous customer items suppliers, adding considerably to the market's development and advancement.
Ecological Influence and Sustainability in Plastic Extrusion
The prevalent use of plastic extrusion in manufacturing invites scrutiny of its environmental ramifications. As a procedure that frequently makes use of non-biodegradable materials, the ecological impact can be significant. Energy consumption, waste manufacturing, and carbon exhausts are all concerns. Nonetheless, sector developments are raising sustainability. Effective equipment minimizes energy use, while waste administration systems recycle scrap plastic, reducing resources needs. Furthermore, the growth of naturally degradable plastics provides a much more ecologically friendly alternative. Regardless of these improvements, further development is required to reduce the ecological footprint of plastic extrusion. As culture leans in the direction of sustainability, manufacturers need to adapt to remain practical, stressing the relevance of continual research study and improvement in this field.
Verdict
In final thought, plastic extrusion plays a crucial duty in modern-day production, especially in the vehicle and consumer products sectors. find out here now Understanding the fundamentals of this process is key to optimizing its applications and advantages.
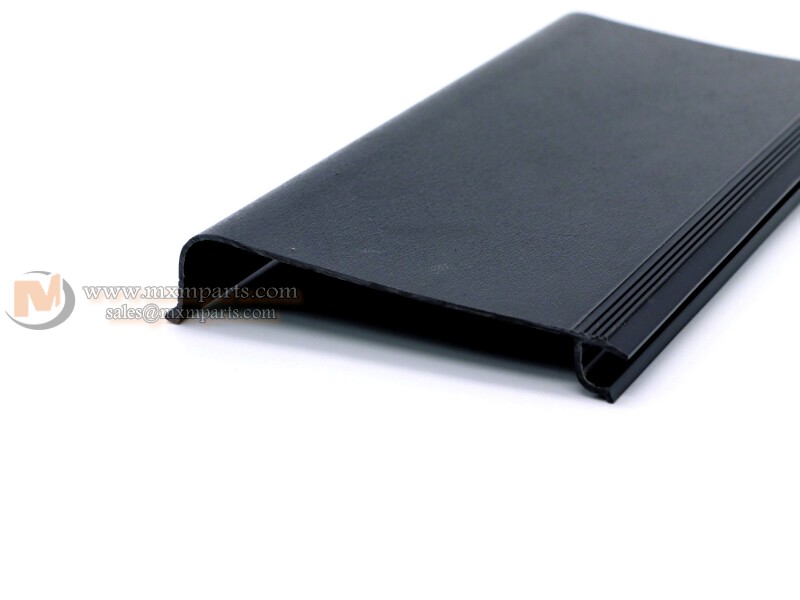
The plastic extrusion process is extensively utilized in numerous markets due to its convenience, effectiveness, and cost-effectiveness.
Building upon the fundamental understanding of the plastic extrusion process, it is necessary to discover the numerous techniques included in this production technique. plastic extrusion. In comparison, sheet extrusion produces large, flat sheets of plastic, which are typically further processed right into items such as food product packaging, shower drapes, and cars and truck parts.An overwhelming bulk of see this here components in modern-day automobiles are products of the plastic extrusion procedure
Report this page